SUBARUは2022年2月9日、エンジン部品であるカムシャフトの研削加工品質をAIで判定するシステムを稼働させたと発表した。同年1月末からSUBARUの群馬製作所大泉工場で運用している。全カムシャフトの品質保証をリアルタイムに実現したことで、従来の抜き取り検査による品質検査と比べて品質保証レベルが上がったとしている。なお、AIモデルは富士通と共同で開発した。AIモデルの導入に合わせて、製造現場でAIモデルを管理するための運用管理ソフトウェア「FUJITSU Manufacturing Industry Solution COLMINA 現場品質AI 運用管理パッケージ」(COLMINA 現場品質AI)も導入した。
SUBARUは、エンジン部品であるカムシャフトの研削加工品質をAIで判定するシステムを稼働させた(図1)。2022年1月末からSUBARUの群馬製作所大泉工場で運用している。導入の効果として、全カムシャフトの品質をリアルタイムに保証できるようになったことにより、従来の抜き取り検査を主体とした品質検査と比べて、品質保証のレベルが上がった、としている。
開発したAIモデルの特徴は、加工中の全カムシャフト(写真1)の品質をリアルタイムに推測する点である。研削設備に接続したセンサーから、全カムシャフトの主軸動力値や振動のセンシングデータを、エッジデバイスを介して収集する仕組み。収集したデータを基に、AIモデルで推測した品質状態が品質基準値の範囲内かどうかを判定し、設備側へフィードバックする。
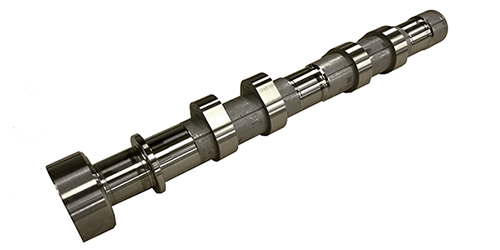
写真1:カムシャフトの外観
製造現場でのAIモデルの運用を支援する仕掛けとして、運用管理ソフトウェア「COLMINA 現場品質AI」も導入した。複数の設備に組んだAIモデルを一元管理できるようにした。予測精度を維持できているかどうかを、AIモデルの推論結果と検査結果を照らし合わせて常に監視する。蓄積した予測結果からAIモデルのチューニング時期を判断し、必要に応じてAIモデルの再学習と展開を実施できる。
実運用前には実証実験も実施した。2019年12月から2020年12月にかけてAIモデルの実証を群馬製作所大泉工場で実施した。1年間の量産での研削加工工程において、AIモデルが高精度に加工品質を予測可能で、実運用でも確実な品質保証が期待できるという結果を得た。
さらに、量産運用を想定した「COLMINA 現場品質AI」の開発・実証を2020年8月から2021年12月にかけて実施した。精度維持のための定期的な確認、精度低下時のAIモデルの再学習、エッジデバイスへの再導入、などを繰り返し実施する仕組みを検証した。AIモデルを組み込んだ各種設備のデータをリアルタイムに処理する仕組みも検証した。
SUBARUと富士通は今後、今回の取り組みをリファレンスとし、カムシャフト以外の部品を含めた群馬製作所全体に横展開を推進する。